Projectmanagement en BRC9
Hoe onveilige producten te voorkomen bij aankoop van nieuwe apparatuur en voldoen aan BRC9?
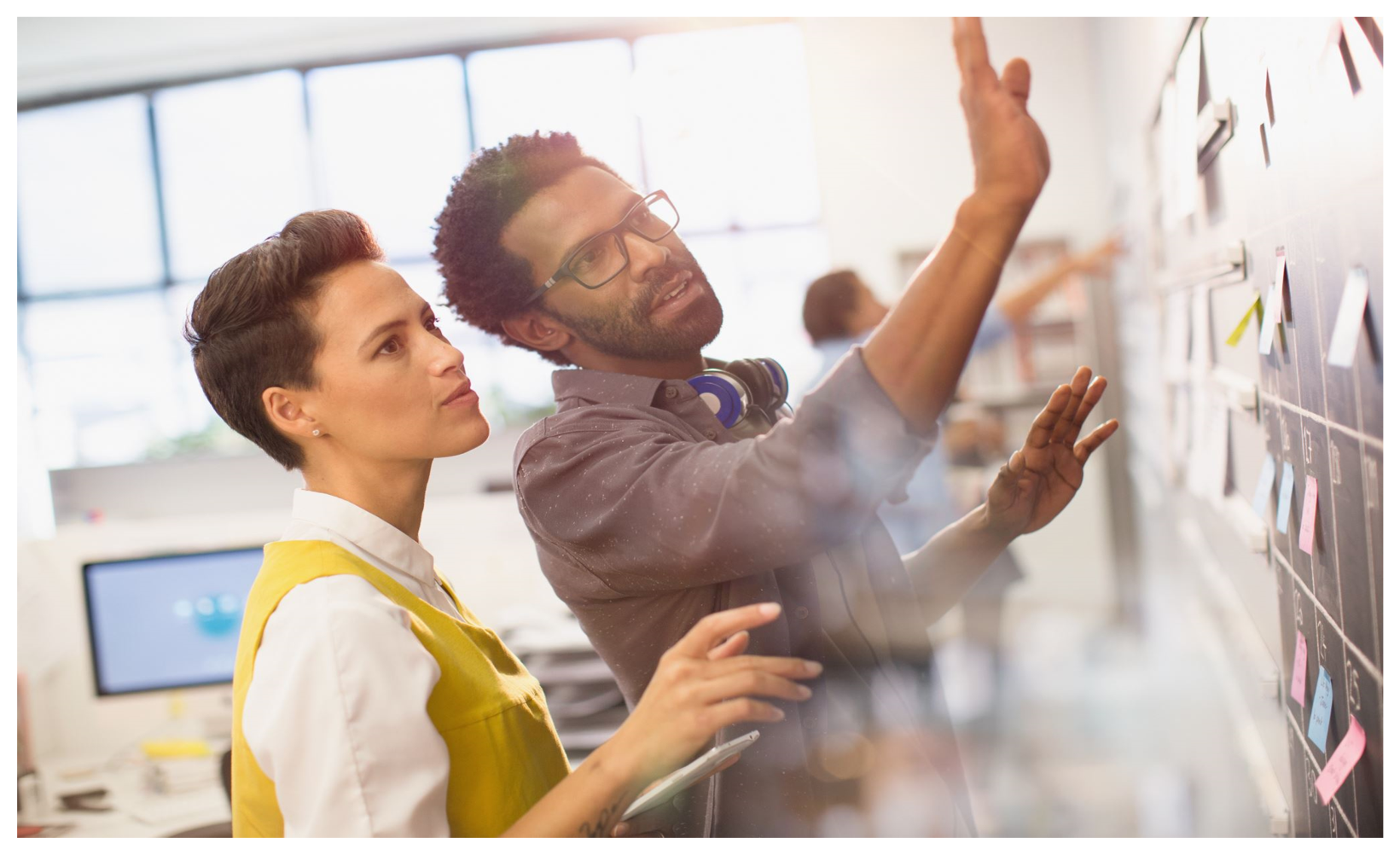
Eén van de onderwerpen die in de BRC9 richtlijn meer aandacht vraagt dan in eerdere versies, is het programma van eisen en de commissioningfase bij de aankoop en ingebruikname van nieuwe apparatuur in een voedingsmiddelenbedrijf. De voedingsindustrie en pharma hebben veel overeenkomsten en leren constant van elkaar. In de pharma is het zogenaamde V-model al jarenlang een veel gebruikt model voor nieuwe apparatuur. Is dit model ook bruikbaar in de voedingsindustrie? Jazeker!
BRC9 eist dat er binnen het vaststellen van het programma van eisen (URS) meer afdelingen betrokken zijn dan enkel de technische projectmanager. De eisen ten aanzien van onder andere productveiligheid, kritische kwaliteits- en proceskenmerken en ontwerp specificatie (hygiënisch ontwerp), dienen vooraf vastgesteld en overeengekomen te worden tussen de verschillende afdelingen, dus ook QA, technische dienst of zelfs de schoonmaker. Als de nieuwe apparatuur uiteindelijk geleverd wordt, dienen deze eisen ook gecheckt en gevalideerd te worden. Dit gebeurt middels een FAT*, installatie, operationele en productie kwalificatiechecks en uiteindelijk een SAT*. Dit klinkt logisch, echter gebeurt dit in de praktijk nog maar zeer sporadisch en niet op een professionele projectmatige wijze. Hierdoor ligt bij het van start gaan van commerciële productie, het niet voldoen aan gestelde eisen op de loer, met verkeerde producten, slechte output en risico op voedselonveiligheid tot gevolg. Met de introductie van BRC9 is het vaststellen van de URS en de gehele commissioning, incl. proces- en productvalaidatie van nieuwe apparatuur verplicht geworden. Grotere bedrijven hebben dit soort projecten uitbesteed aan een projectmanagement afdeling of bureau, echter bij middelgrote en kleine bedrijven komt deze taak vaak bovenop de operationele taken van b.v. technische dienst of inkoper te liggen met alle gevolgen van dien.
Een praktisch model is dan wenselijk en het V-model biedt uitkomst, tenzij pragmatisch geïmplementeerd. Alvorens alle eisen te gaan vastleggen in en URS, is het maken van een impactanalyse essentieel. Hierin bepaalt u welke stappen vanuit het V-model doorlopen moeten worden om te voldoen aan de BRC9 richtlijn. Het lijkt logisch dat nieuwe apparatuur waarin een OPRP of CCP ** een rol speelt, dit model geheel moet worden doorlopen. Is dit ook voor ondersteunende apparatuur nodig bij een HVAC installatie, of het realiseren van een handenwasstraat bij de ingang van een low-care productieruimte? Stap 1, na het benoemen van een projectdoel, is dus het doorlopen van de impactanalyse. Dit kan veel werk besparen.
Mijn ervaring is dat, hoe eerder in het aankoopproces nagedacht wordt over het vaststellen van eisen en deze ook projectmatig in teamverband benadert, dit hoge onnodige kosten kan voorkomen en uw apparatuur, tijdig en snel operationeel is, tegen de gewenste (voedselveilige) specificaties . Heeft u ondersteuning nodig bij het uitvoeren van een impactanalyse of bij het vaststellen van het programma van eisen of het implementeren van het V-model in uw kwaliteitshandboek, neem dan gerust contact met mij op via rene@rmb-consultancy.nl of op 06-20136745.
* FAT- Factory Acceptance Test en SAT - Site Acceptance Test
** OPRP - Operational Prerequisite Program of basisvoorwaarde programma en CCP - Critical Control Point
#constructingopportunities #OPRP #CCP #HACCP #BRC9 #Vmodel #foodsafety #commissioning #impactanalyse #projectmanagement #food #GMP #quality
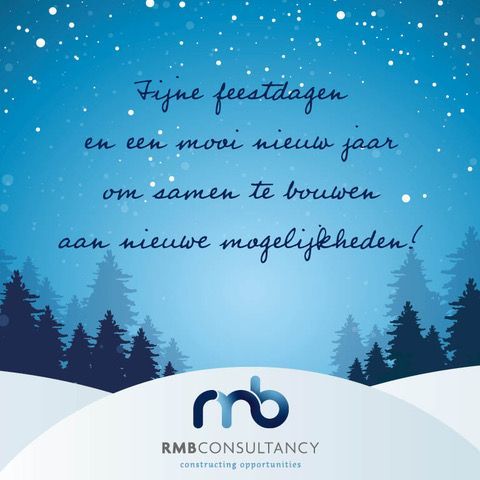

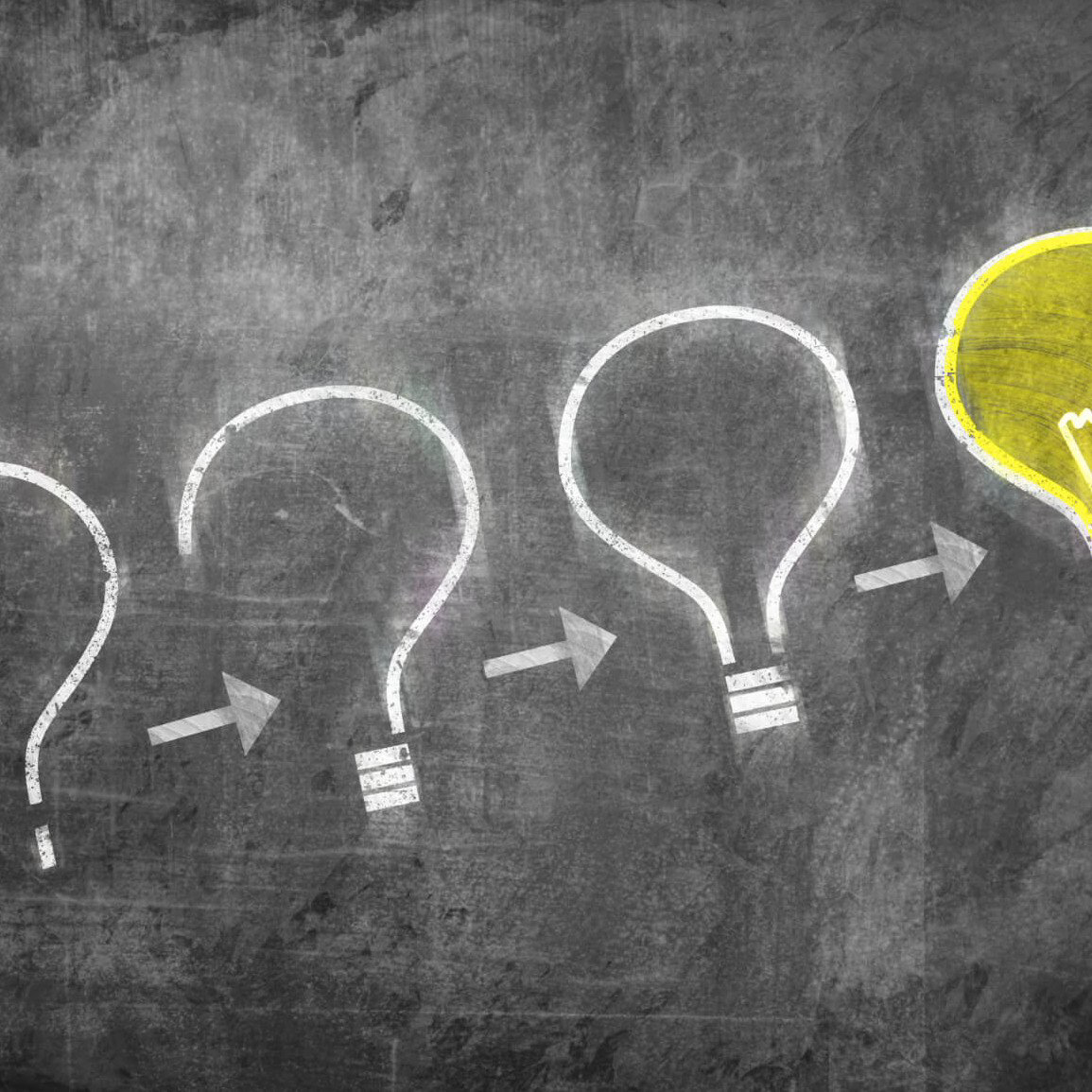